Gear Closet
Gear Closet is a functional, lightweight, packable approach to storing backpacking and camping gear. Constructed from half inch plywood, dowels, and duct webbing, I created a storage solution that is flexible and fits my needs as both an outdoor enthusiast and college student constantly on the go.
Designed in AutoDesk Fusion 360 and made on the ShopBot CNC.
Ideation
I knew I wanted to create something functional and useful for my own life that could apply to others. After being prompted with creating an “heirloom item" for my digital fabrication course, I considered my love for the outdoors (backpacking, hiking, etc.) as a non-tangible heirloom that I could create something physical for. My initial ideas ranged from storage, to tools, to camp chairs, and more. The ideation process included lots of sketching and, once realizing storage was a route I wanted to seriously consider, research of current solutions for gear that other people in the outdoor community had explored.
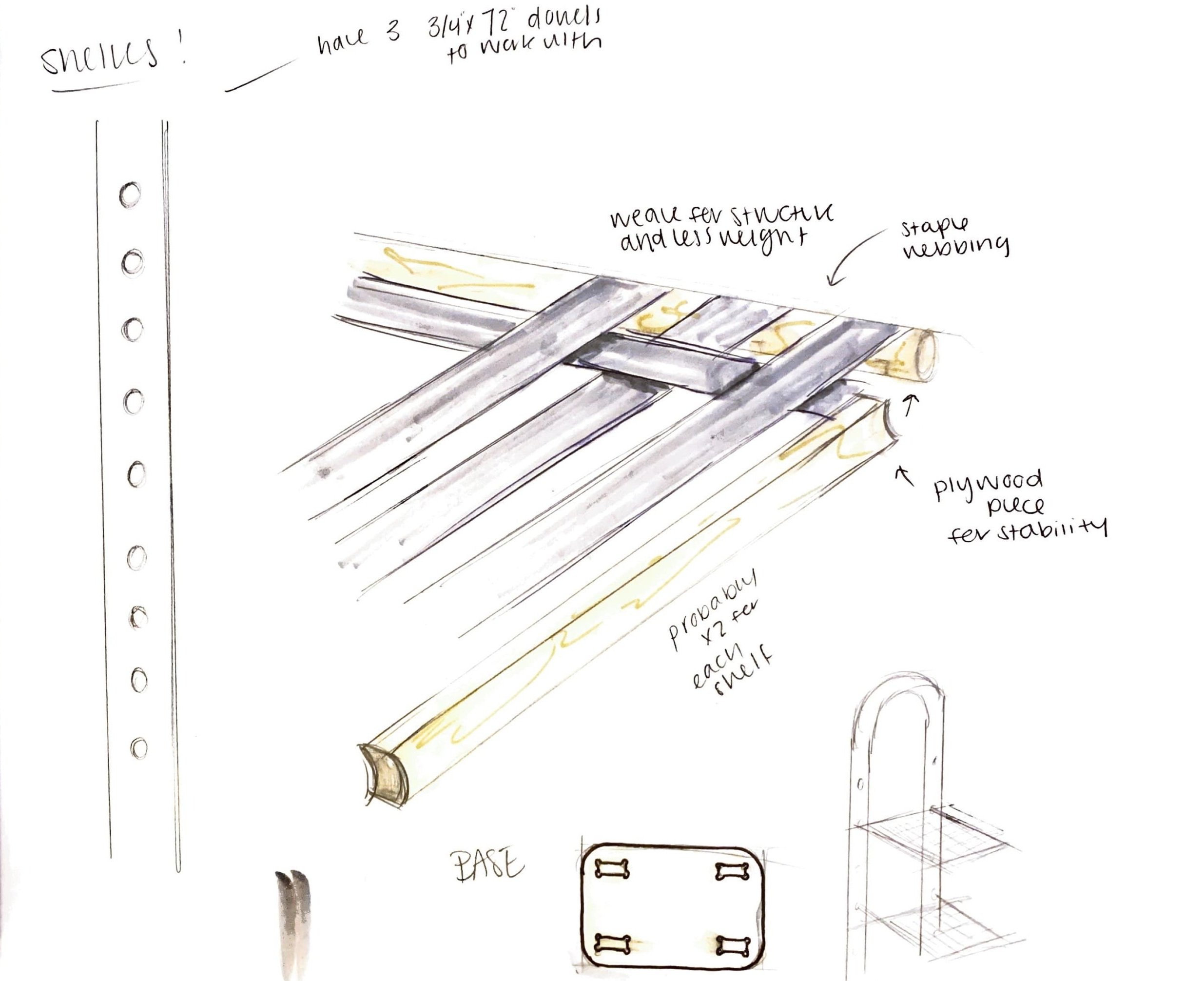
Design
After considering a variety of forms and methods of storage in my ideation, I began with low fidelity modeling in cardboard to conceptualize the form I wanted my piece to take. I measured all the gear I wanted the closet to hold, scaled down those measurements, and made models of the biggest pieces of gear that needed to be accounted for. After low fidelity modeling, I moved to AutoDesk Fusion 360 where I used the sketch function to draw out the 2D file the CNC would use to cut the pieces. I spent time here thinking about the relationship of the gear to the form to account for weight distribution and visual balance.
While initially overwhelmed by options and design possibilities, I was able to narrow down my ideas once I started thinking about the physical items I wanted to prioritize as the constraints for designing my piece. I also spent a lot of time looking into CNC projects, flatpack furniture, and talking to former Stamps student Ella Rocker about her previous work in furniture.
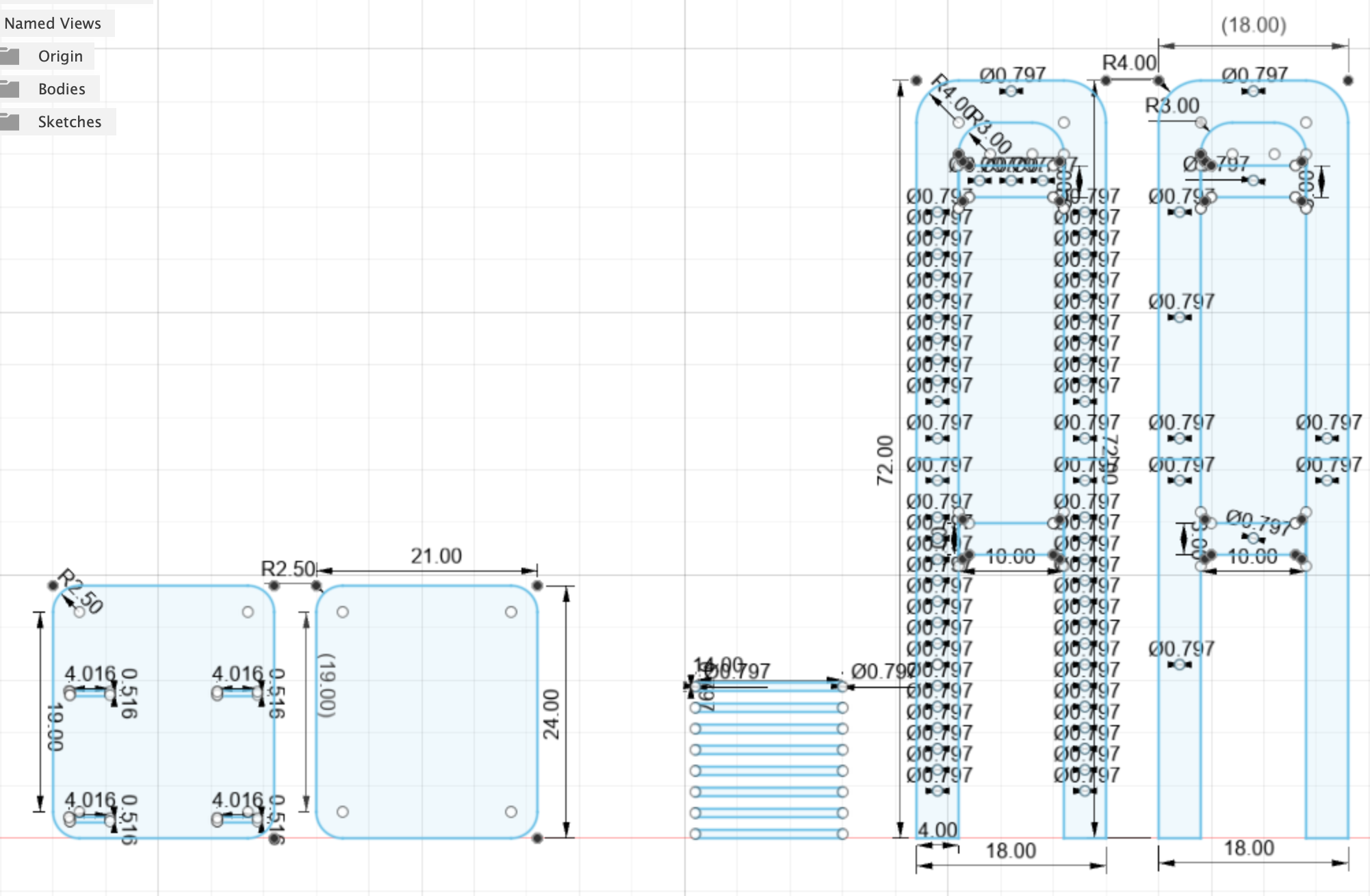
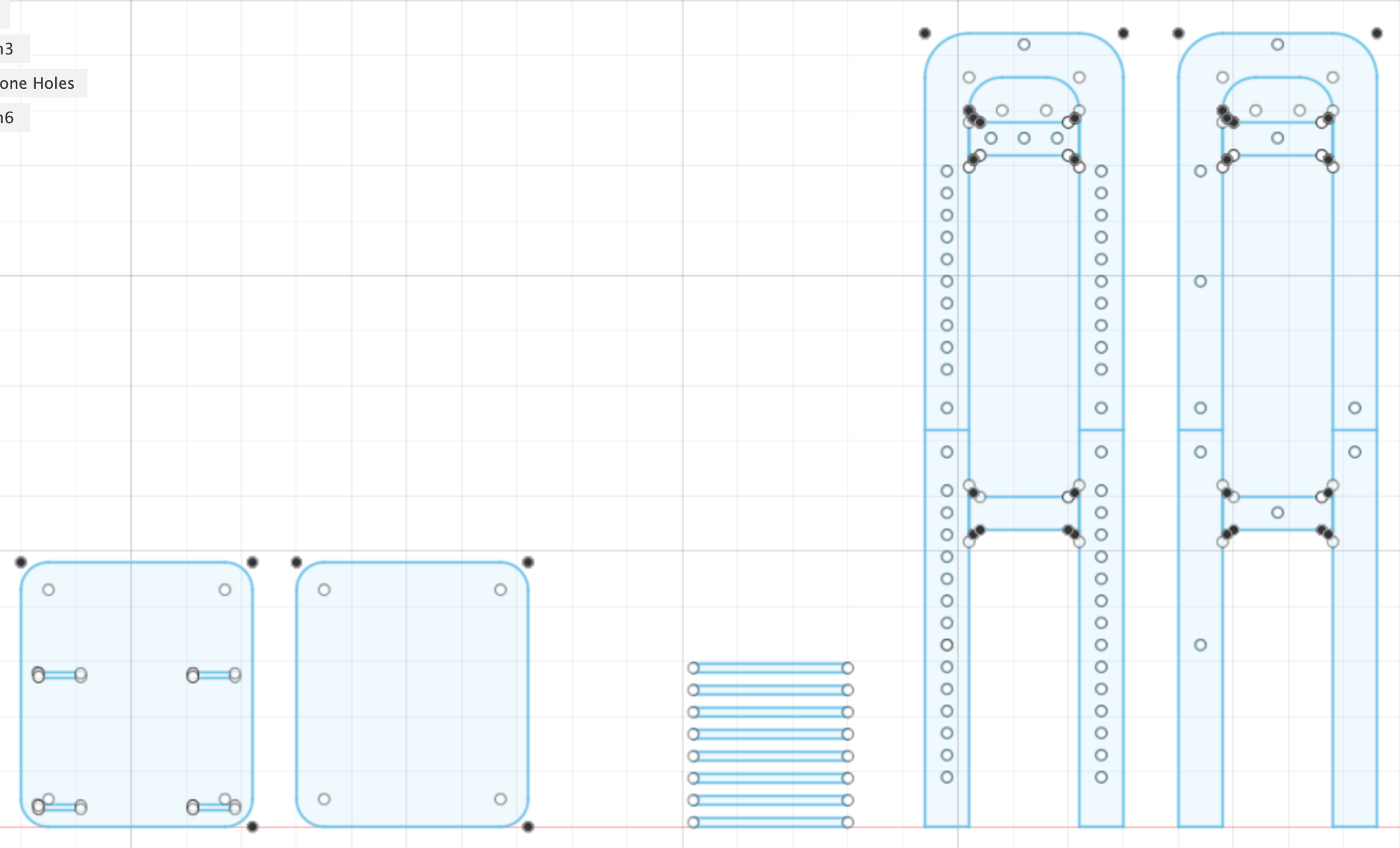
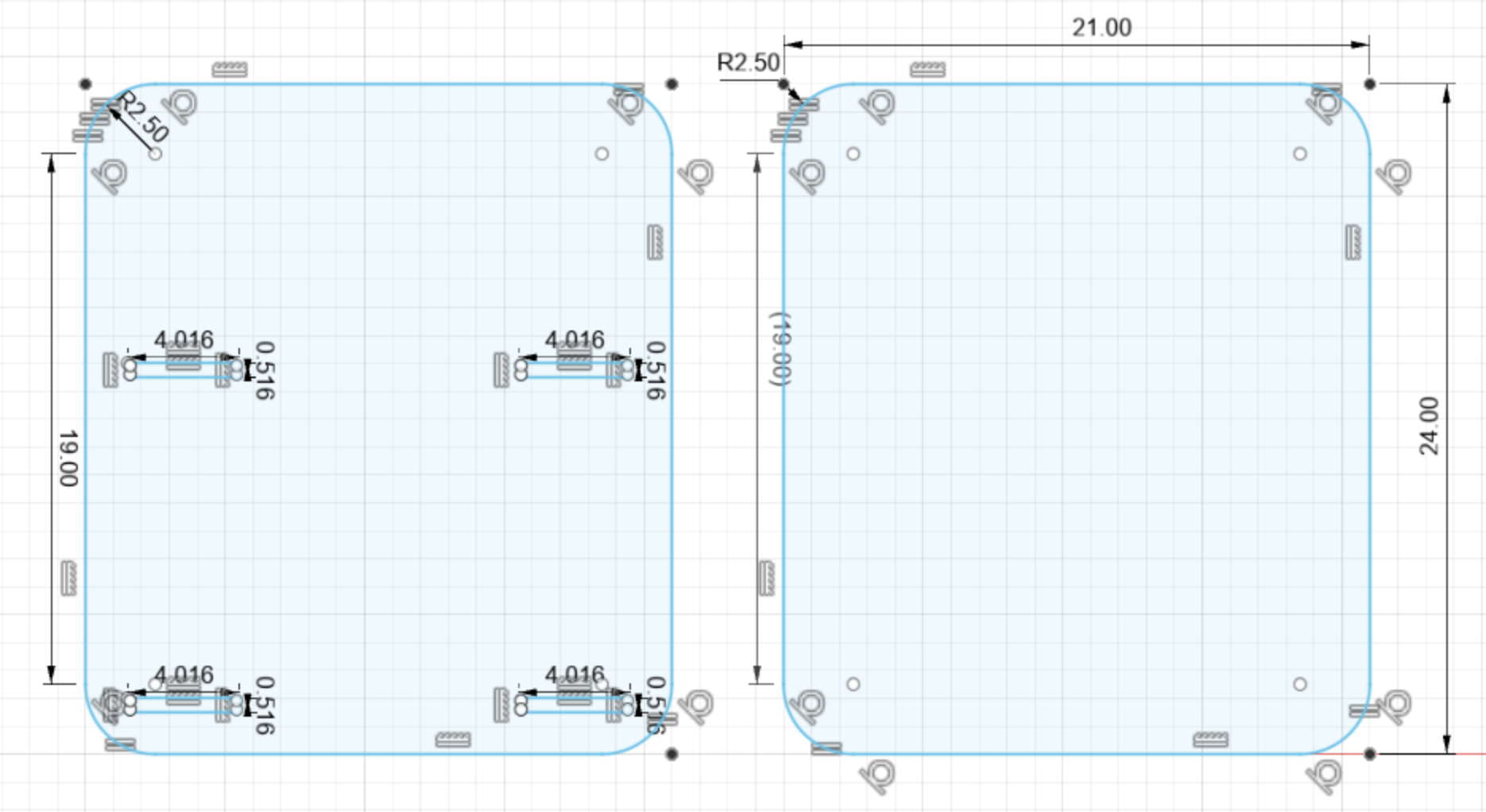
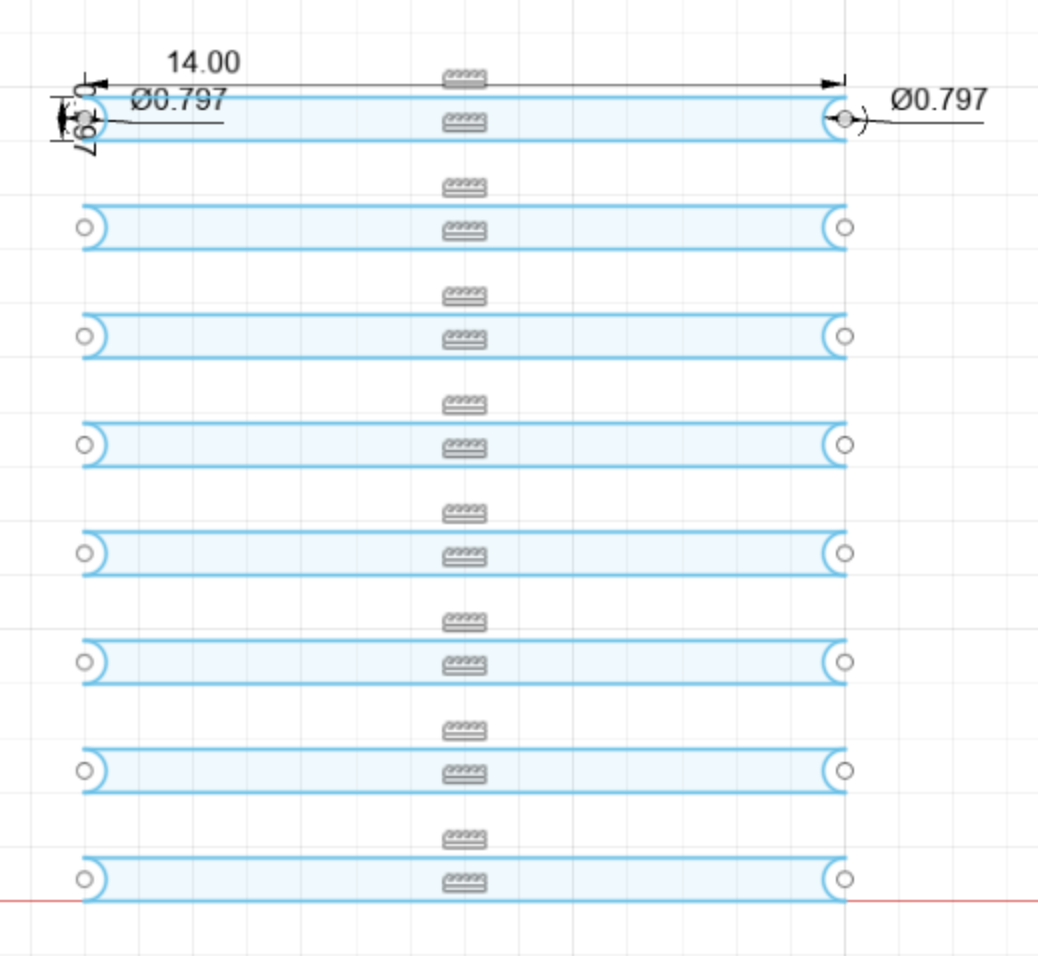

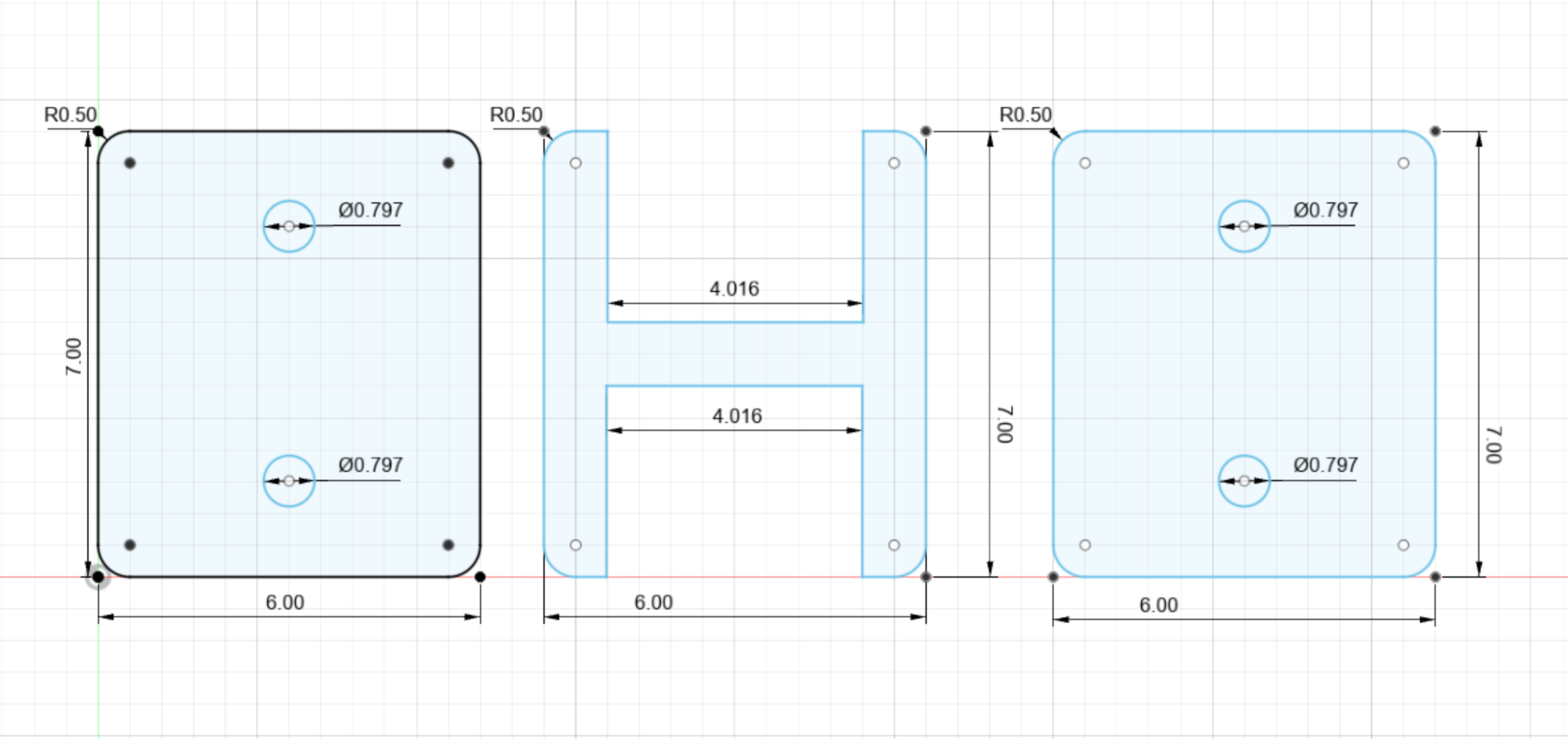
Fabrication
After converting my Fusion designs to DXF files, I used a ShopBot CNC to cut out the pieces of my closet. After removing the pieces from the plywood, I dry fit all my pieces and realized I had some adjustments to make. I had made a few errors in measurements and had to hand sand some of the slots for other pieces to fit into.
After adjusting my slots, I assembled my support joints and starting building shelves from dowels, CNCd pieces, and duct webbing assembled with a staple gun.
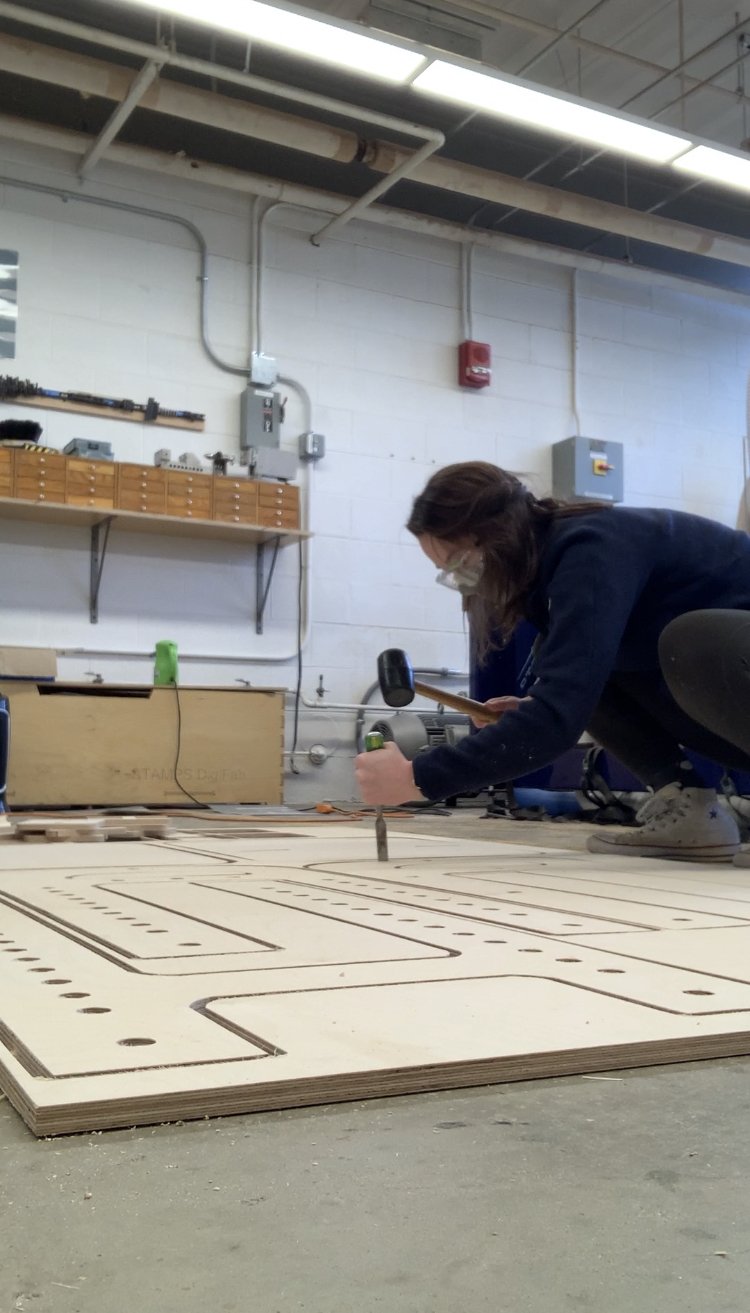


Timelapse of me building the adjustable shelves for the Gear Closet.
Build
A priority of this build was packability and flexibility. To highlight the building process and packability, below are images of me constructing the closet from the base up. I ran into some minor structure issues when assembling, but found I was able to adjust with dowel lengths.
The entire piece takes approximately 5-10 minutes to assemble and is made up of 19 pieces (including each shelf as a “piece”).
I look forward to expanding on and improving this project going forward. It was a reminder that physical modeling can be a great tool to get to the solution to a given problem and pushed my abilities in new fabrication processes.